Achieving scale and efficiency in custom manufacturing
The manufacturing industry is driven by—and benefits from—productivity and efficiency improvements. Manufacturing largely accomplishes this through automation, manufacturing line layout and just-in-time production, among other innovations.
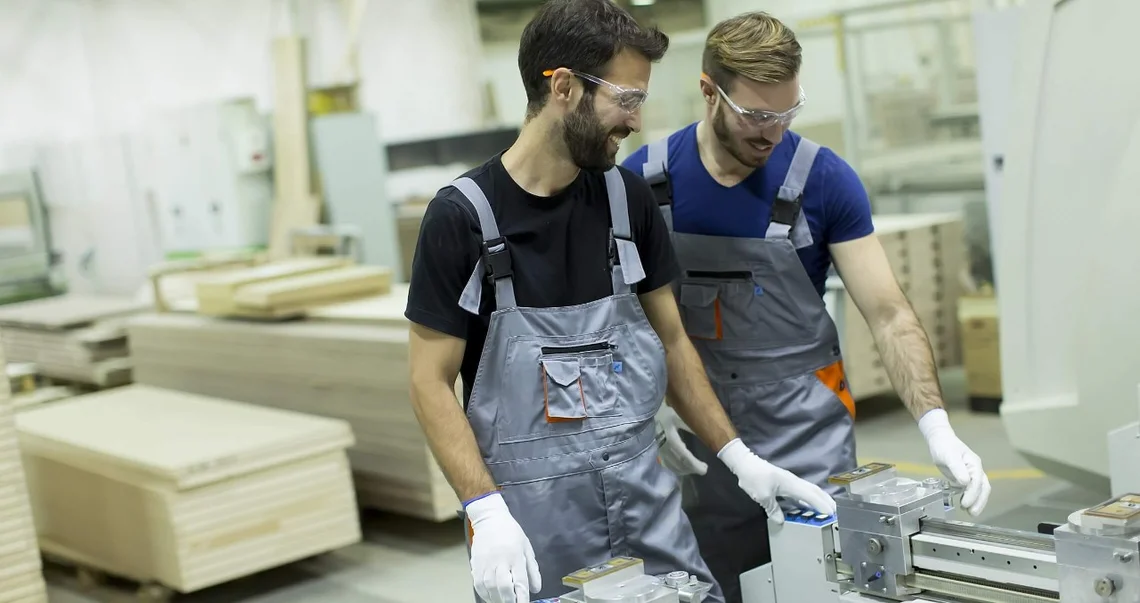
But custom manufacturers may not be able to apply all of these solutions. Fortunately, companies can still scale into a high-volume business with a higher degree of customization by identifying and implementing improvements in these four areas.
Challenges in custom manufacturing
Like with traditional mass manufacturing, tight profit margins in custom manufacturing necessitate efficiency. But the business model, which is based on individual attention to customer requirements, limits how much consistency can be built into operations.
Custom manufacturing emphasizes unique, quality products. But sustaining quality is difficult when almost every product has different specifications. In mass production, you can measure and tighten the variances across production segments—but not with customized products.
In addition, customers still expect rapid turnaround times. Clients are willing to wait a little longer for customized products—but not too long. And haste makes waste.
1Leverage employees
One way your firm can scale and build a strong custom manufacturing system is by more efficiently and effectively deploying your employees at all levels. Provide strategic—not just task-oriented—job descriptions that tie each employee's role to company performance and communicate expectations for each job type and role. This will help you assemble more flexible teams. Craft clear standard operating procedures, or SOPs, that outline how a job is done so each employee performs that job the same way. Update these SOPs when the process changes to ensure they remain efficient.
Train employees wisely. In addition to taking advantage of any training that comes with software system upgrades, have management poll employees and line managers to determine what additional training they need. In doing so, management can obtain meaningful guidance on how and when to provide this training in the least disruptive manner. In a customized setting, it can be inefficient and ineffective to cross-train many employees on the same process. Instead, consider cross-training by product types or skill sets to reduce the project ramp-up time.
2Invest in suitable technology
Another way to scale is to mine data from your processes. Use this data to help identify improvements and make decisions using industrial sensors tied into analytics software. These basic yet state-of-the-art components are part of the Internet of Things, or IoT, and can sense and collect data across production.
Using the information the analytics software provides can also increase your overall customization agility. You can go a step further and upgrade to predictive analytics software, which forecasts trends and maintenance needs. This software can enable you to address issues before they become major problems. It's one of many ways AI can monitor and improve production and quality control.
If feasible and where applicable, your firm can also switch to 3D printing or other rapid tooling processes to both simplify production and reduce production times.
3Implement operational improvements
Because of the sheer number of processes involved in customization, there isn't as much room in a customized manufacturing system to reduce waste. But reducing any waste in these processes will positively impact your ability to scale. According to Reliable Plant, reducing waste also improves process agility. Fewer materials or actions reduce the production time, which allows you more time for value-added customization steps and increased throughput.
In creating or revamping your SOPs, examine each process—from order entry to final shipment—to determine where you can squeeze out waste and shrink lead times.
4Strengthen your sourcing
Because customization levels often require components from multiple manufacturers and suppliers, many custom manufacturing firms don't build a strong, integrated supply chain. But a highly dependable and integrated supply chain can drastically shorten production runs, allowing you to increase personalization or scalability.
Because quality is paramount, deepen relationships with suppliers that consistently deliver high-quality components on time and on budget. This reduces or even eliminates the need to inspect incoming materials without risking reworks or returns.
The bottom line
It's possible to scale your custom manufacturing enterprise. To do so, focus on the personnel protocols, technology implementation, production improvements and supplier relationships that will drive efficiencies while maintaining the service and quality your customers expect. Speaking with a trusted business partner can help you understand your company's needs and capabilities to improve your operations at scale.