Combating construction inflation costs
Since the beginning of the pandemic, construction has felt the squeeze, as materials rose in both costs and scarcity. Then, another problem—inflation. Inflation continues to impact the industry and exacerbate supply chain problems.
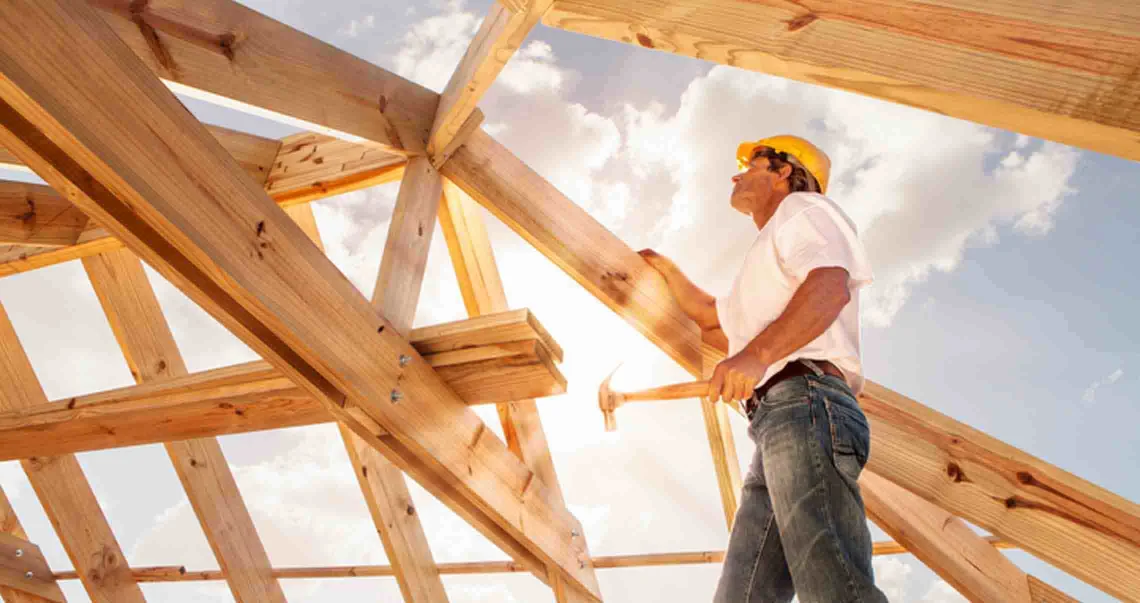
In December 2022, the Associated General Contractors of America, or AGC, published a Construction Inflation Alert report (PDF) highlighting the impact of inflation, input costs and supply chain issues across the industry. Here's what they found in the report, along with strategies you can use to curb the impact of inflation.
Construction inflation costs
The AGC report tracked construction input costs from August 2020 until October 2022. According to the report, the consumer price index, or CPI, "declined at the beginning of the pandemic but began climbing on a year-over-year basis in August 2020. As prices rose at unprecedented rates for a wide range of construction inputs, the index accelerated steeply, rising at a record-high annual rate of 24% in June 2021." Furthermore, year-over-year increases remained at or above 20% from May 2021 through April 2022. During this period, overall nonresidential construction costs increased by more than 11% between October 2021 and October 2022.
On top of higher prices, the construction industry also faced delays receiving materials through supply chain disruptions and employees missing work due to COVID-19. On the plus side, port congestion has cleared up on the West Coast, and procurement for lumber and steel products has returned to pre-pandemic wait times. On the downside, cement and concrete products, computer chips, construction vehicles, transformers and semiconductors are still facing bottlenecks and long wait times.
Factors leading to higher costs
Construction material supply chains faced a storm of issues over the past couple of years. First, the pandemic caused key factories to shut down due to outbreaks, so there was no reliable supply of goods. International trade suffered even worse, with shipping shutdowns around the world and key ports facing bottlenecks.
In addition to cost inflation, national trade policies passed on Chinese goods from 2018 to 2020 had increased current prices for many materials. Logistics and supply chain fraud is also an ongoing issue.
Since then, the ongoing turmoil between Russia and Ukraine has created an unpredictable landscape in regard to oil dependency and previously established trade agreements.
Construction material cost forecast
Costs are expected to remain high or potentially escalate throughout 2023. Factors including Russia's cutoff of natural gas to central and western Europe, sanctions against Russian oil, European demand for diesel fuel and the worldwide limitation of supplies have affected the cost of construction plastics, glass and other fuel-based materials.
Prices have seen dramatic shifts in either direction, making it difficult for construction businesses to reliably predict the cost of materials. For example, according to the AGC report, the Producer Price Index, or PPI, for steel mill products dropped 6.6% from September to October but jumped 10.5% between April and May.
Keep in mind that the construction industry is vulnerable to supply shocks and sudden price increases as you prepare your risk management plan and construction material cost forecast for the remainder of 2023.
Strategies to combat construction inflation costs
Global supply chain struggles, military conflicts and tariffs are out of your control, but there are some strategies you can use to offset the hit on your bottom line.
- Be realistic when quoting project costs. When you negotiate new contracts, make sure to adjust your rates for the higher costs. Let your clients know about the ongoing situation, and clearly show that the extra charge is going to materials, not profit.
- Update existing clients about the situation. If you've already signed onto projects and costs have spiraled since, reach out to see if there's any room to negotiate. The client may be willing to accept a higher price if you promise you'll still work to complete their project in a timely fashion.
- Add a price-adjustment clause to contracts. To protect yourself against future construction cost escalation, you could add a price-adjustment clause to future projects. This way, if materials jump up by a certain amount (set in the contract), you get to increase your price, too.
- Consider buying materials early. If you stock up on key construction materials, you're protected against future increases and supply disruptions. There are downsides to this approach. For example, you'll likely need to spend cash upfront and pay for a place to store the materials. However, if your top priority is to guard against supply shocks, this could be worth it.
- Budget for construction inflation costs. Construction cost inflation is an ongoing risk. Make this part of your business plan and be pleasantly surprised if prices don't go up, rather than assuming things will stay at the same level.
Business owners should expect to deal with inflation and all its consequences for some time to come. Blunting the impact comes down to both understanding the sources of the problem and developing nimble strategies to counteract them.