How predictive maintenance optimizes production and profits
Maximizing assets and achieving efficiency are key goals for virtually every business—and these are exactly the outcomes that predictive maintenance, or PdM, seeks to achieve.
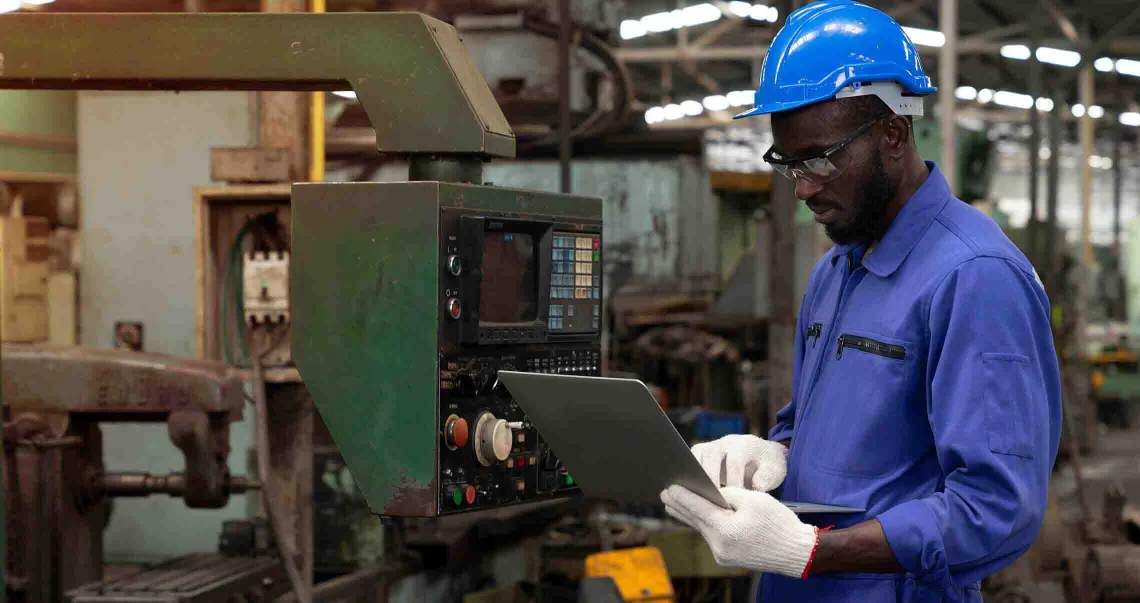
Still, realizing these benefits depends on how well you align predictive maintenance tools and techniques with your business strategy. Understanding what PdM entails and how to prepare for success can be the first step in a journey toward a stronger bottom line.
What is predictive maintenance?
PdM is an approach to anticipating the maintenance needs of critical equipment and machinery. It requires analyzing historical and real-time operational data. When the analytics are accurate, you can perform maintenance just before a failure is likely to happen—but only as required. In this way, PdM differs from routine or preventive maintenance, which can run the risk of forcing equipment offline unnecessarily.
Because planning for critical maintenance minimizes downtime, one key immediate advantage is cost reduction. In tight-margin sectors, even just a few hours less downtime can make a substantial difference. Also, manufacturers can avoid situations where small repair needs morph into larger, more expensive ones. Extending the life of critical machines and equipment can go a long way in better managing capital and boosting ROI.
The capability to anticipate downtime can also help to optimize across operations in ways that can impact revenue, cash flow and the customer experience. Knowing when the replacement of equipment or parts might be necessary can make budgeting and financing easier. By getting ahead of potential service degradation, your business can manage quality assurance and control issues. You can also temporarily shift personnel tied to the machine needing service to other functions or allow them time off to avoid waste in the labor budget. Plus, predicting when machines are most likely to fail can improve safety and risk management.
How predictive maintenance works
PdM uses an algorithm that analyzes sensor data. To develop this algorithm, engineers must gather data under both healthy and failing conditions. Consistent, high-quality data collection is crucial.
Once they have data, the engineers then use tools to preprocess it and extract features. The features indicate the difference between healthy and faulty operation and are key to the success of PdM.
These features are used as input in a statistical or AI algorithm. The algorithms should detect anomalies, identify faults or estimate remaining useful life. AI and machine learning are particularly helpful because they can detect even the slightest inconsistencies or deviations and learn from patterns and correlations, which helps them predict PdM needs with increased precision as time passes. In the future, AI algorithms may even be able to pinpoint the specific components as risk, allowing for more targeted and effective maintenance.
Identifying essential factors for success
Predicting the need for repairs fundamentally relies on the continuous monitoring of process-essential equipment during operating conditions. Data from other functional areas may also be necessary, such as inventory and work order data, depending on the use case. Companies harness technologies such as the Internet of Things, or IoT, and machine learning, as well as other integrated systems to perform this data collection and processing.
Manufacturing environments are rife with opportunities to employ methods that anticipate breakdowns and machine failures. For example, sensors can help you monitor pressure, load, fuel usage and even operational climate. Data on audio frequencies can help determine whether bearings are lubricated or valves are leaky.
While technology is crucial, people can make or break the success of predictive maintenance. Ideally, managers must understand business goals well enough to set meaningful priorities and make sound decisions about where and how predictive maintenance can be used. Reporting staff should be made aware of objectives and issues relevant to their duties. Further, IT staff needs to be well-versed in not only setting up the requisite systems but also evaluating the opportunities and threats within the technology. Communication channels between all levels should seek to empower feedback and process improvement.
Getting started
Setting up for predictive maintenance can require a commitment of capital and other resources. To make the investment worth it, choose the business operations and use cases that make the most sense for implementation. Begin by identifying durable equipment in which potential failures may impact operations the most. Consider which machines and relevant tools can provide quality real-time data with enough lead time to flag problems before they become unmanageable.
Predictive models need quality data points to collect and deliver accurate and meaningful insights. Your IoT setup and automation capabilities should allow live and reliable tracking of machine statistics. The real-time monitoring of asset condition and operations can involve collecting any data that might shed light on conditions that diminish the optimal equipment performance. Plan to ensure data quality with any necessary data cleaning and preparation.
Keep in mind that some failures can't be predicted. A natural disaster or human error can take otherwise pristine equipment down in the blink of an eye. So, leave some room in your operational planning for good old-fashioned reactive maintenance while prioritizing a proactive, predictive approach.